Last Updated APRIL 2024
Sustainability: a central tenet shaping the future for manufacturers
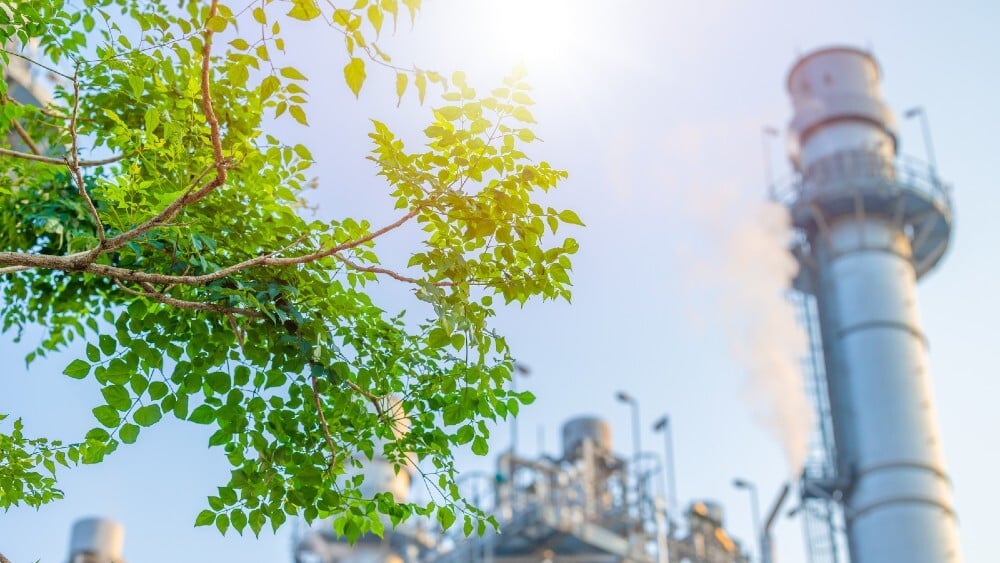
According to new research1 by PwC and the World Economic Forum (WEF), businesses could unlock annual savings of around $2 trillion a year across the global economy by implementing cost effective energy efficiency measures. Therefore, embracing sustainability – and resource efficiency, in particular – is not only great for the environment but also essential for the long-term viability and success of industrial companies.
But it’s not just about cost savings. Sustainable manufacturing promotes local sourcing, reduces dependencies on distant suppliers, and enhances supply chain resilience against disruptions. Operating more sustainably also helps to appease increasing eco-aware stakeholders. Today, investors, shareholders, and customers expect the companies they work with and buy from to be doing all they can to produce things responsibly, protecting people and planet in the process.
So, what kinds of things can manufacturers do to take action? Well, industrial manufacturing has historically been a significant contributor to environmental degradation – using many valuable resources and creating lots of waste. Companies can minimise their environmental footprint by optimising their processes and adopting measures to reduce their consumption of energy, water and other natural resources.
The quest for sustainability drives innovation. Digital technologies and enhanced data analytics are helping to revolutionise manufacturing, enabling real-time monitoring, predictive maintenance, and the optimisation of processes. For example, specialist scheduling and data collection software can help firms plan, optimise and adjust maintenance schedules in line with real-time production-floor conditions, reducing unnecessary activities. Integrated work-management tools and real-time communication apps can flag any potential risks or issues and alert the right people to take appropriate action.
The adoption of sustainable materials, bio-based alternatives, and eco-friendly substitutes is on the rise too, with many companies exploring innovative materials that are recyclable, biodegradable, and have a lower environmental impact.
The shift towards a circular economy model, where products are designed for longevity, repair, reuse, and recycling, is gaining momentum. Industrial manufacturers are redesigning products and processes to minimise waste and maximise resource efficiency.
There’s also growing shift towards renewable energy sources, such as solar, wind, and hydroelectric power, to power industrial manufacturing processes. Renewable energy not only reduces carbon emissions but also offers long-term cost savings.
At Kimberly-Clark Professional™ we’ve realised this need for energy security. As part of our global decarbonisation strategy, Kimberly-Clark has made significant strides in making use of renewable energy, for example. It has signed a Power Purchase Agreement with Octopus Energy Generation to build a £75 million onshore wind farm in Scotland which generates around 80% of the firm’s UK electrical power needs.2 The turbines deliver carbon emissions savings of 55,625 million tonnes of CO2 equivalent per year, the equivalent to taking more than 38,000 passenger vehicles off the road.
As a large-scale and energy intensive industry, we are also developing on-site solar power and green hydrogen projects3 to make further use of clean energy across our facilities. “In Spain, we are working with Edison Next to develop a huge solar photovoltaic plant which will power our production facility in Salamanca. It will also help to reduce our carbon footprint by 1,759 tonnes of CO2 a year, the same amount as is produced by almost 2,000 homes in Spain,” says Oriol Margó, Sustainability Transformation Leader at Kimberly-Clark.
Kimberly-Clark Professional is proud to support many manufacturers as they continue to roll out sustainable practices in their facilities. Unlike rags and laundered cloths – which can retain hazardous lead and contribute to cross-contamination and generate more waste in landfill – our range of WypAll® products help our clients deal with all manner of cleaning requirements in industrial settings, whether absorbing liquids faster, removing oil and grease more efficiently, or dealing with solvents and harsh chemicals.
Siemens Energy, a company committed to improving health, safety, processes, costs, and sustainability as part of its approach to agile manufacturing,4 is using WypAll® Forcemax™ to help reduce its paper product usage. The industrial cloths are specifically designed to cope with tough wiping tasks, absorbing 40% more oil, five times faster than rags or laundered cloths.
Similarly, the luxury catamaran manufacturer, CATANA Group is using WypAll X® to support its meticulous boat-building process where wiping cloths are indispensable for several critical tasks, from waxing moulds and cleaning excess glue or resin to the delicate work of degreasing before gluing.
The WypAll® Reach PLUS™ Single Sheet Centrefeed Dispenser also helps manufacturers save up to 50% on their paper consumption. Meanwhile The RightCycle™ Programme provides a closed loop service so that each used towel is turned back into new Kimberly-Clark Professional™ paper products, helping customers reduce their waste by up to 25% and increase their recycling rate by up to 5%.5
For manufacturers, sustainability is no longer a ‘nice to have’ but an imperative that is heralding a new era of responsible and resilient industrial practices which is good for workers and good for the planet.
1 https://www.weforum.org/press/2024/01/wef24-action-on-energy-demand/
2 https://www.kcprofessional.com/en-gb/workplace-insights/sustainability/what-our-decarbonisation-journey-means-for-your-business
3 https://www.news.kimberly-clark.com/2022-08-31-Kimberly-Clark-and-Carlton-Power-Enter-Partnership-Agreement-to-Launch-Breakthrough-Green-Hydrogen-Project-in-Barrow
4 https://www.sciencedirect.com/science/article/abs/pii/S0925527398002229
5 Based on UK offices per person average kilogramme of waste.